Capability building amid crisis in Industry 4.0
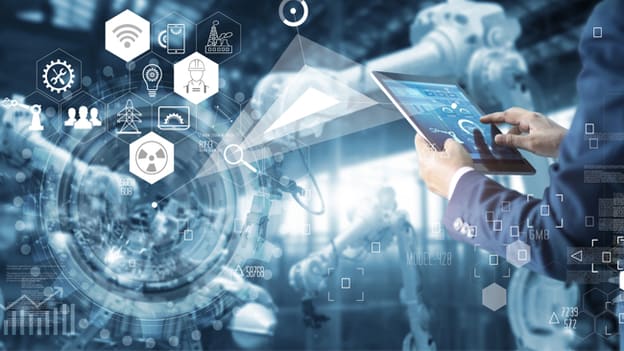
Our ability to enable the blue-collar workforce to acquire skills relevant for smart factories of today and the future is among the biggest challenges for Indian HR leaders in manufacturing.
Within the new manufacturing ecosystem ushered by the Fourth Industrial Revolution, factories around the world are getting smarter and the need for building a new set of capabilities is also growing rapidly. The changes we are now seeing on shop floors are not just about smart machines and new embedded technologies such as IoT (Internet of Things) connected machines, artificial intelligence, robotic process automation, and data science, but more importantly, a new set of human capabilities to analyse and use the knowledge to deliver more value.
The transformation happening in the manufacturing sector is not just about our ability to adopt new technologies but also building new sets of skills to help us use them to our advantage. The benefits that are flowing from these changes are also transforming how we measure the competitiveness and the ability to differentiate ourselves in the global marketplace. Adoption of these new technologies is now helping us run the machines with minimal or zero downtime, improve the quality and productivity of both machines and people, customise products and develop new ones, and access new customers and markets. With such sweeping transformations taking place in the manufacturing sector, the question is not whether we wish to be a part of the Fourth Industrial Revolution but how quickly can we change and more importantly how do we build the human capabilities to drive and sustain this.
Even though India’s manufacturing sector opened up to the idea of globalisation towards the end of the last century, it continued to lag in terms of global manufacturing practices and building a skilling ecosystem that can support this, until recently. The transformation in India that we are seeing today was largely driven by the engineering sector, particularly the automotive industry where completely robotised paint shops and welding machines started popping up a decade or so ago. This apparent delay can be attributed to the high cost of technology not supported by economies of scale that can justify heavy investments that Industry 4.0 demands. However, today even though capital-intensive smart manufacturing is becoming increasingly commonplace, we are facing a new kind of challenge in terms of finding the right kind of skilled manpower in sufficient numbers to run these factories.
This challenge is being addressed at multiple levels both within the limited sphere controlled by manufacturers and the larger ecosystem involving academia (mainly engineering colleges) and vocational training institutions.
Large manufacturers for example are going the extra mile by helping their own downstream supply chain partners to adopt a greater level of automation and building capabilities to run them. Further OEMs (who supply the machines) are also adding their strengths to build new and relevant capabilities by training the existing workforces to upskill themselves on the job. These are at best incremental efforts and may not be enough in the long run.
To fill this new kind of skill gap in our manufacturing sector, there is an urgent need to tackle this within our educational ecosystem i.e., engineering colleges and vocational training institutions. For example, dedicating the final year of a four-year engineering graduate program to building capabilities relevant to Industry 4.0 will be a very effective first step in this direction. Manufacturing employers committing an entire year to building the capability of their new hires cannot be sustained in the long run. Therefore, building a massive skill pool of relevant workforce has to start from our colleges and polytechnique or vocational institutions. Industry for its part can work with them to make their academic curriculum relevant and up to date.
Today, India produces in excess of 1.5 million (1) engineering graduates each year, with only a fraction of them capable of fitting into the job market. A recent story published by Washington Post (2) even said that several engineers and MBAs in India are being forced to take up manual work due to the alarming increase in job losses caused by the COVID-19 pandemic. To some extent, such dire situations can be addressed effectively by correcting the curriculum and making them more relevant to what the industry needs.
This is also a great opportunity for Industry, Academia and Government to collaborate and ensure that they work in unison to make India a formidable force in the global manufacturing arena.