Breed of IR managers have vanished
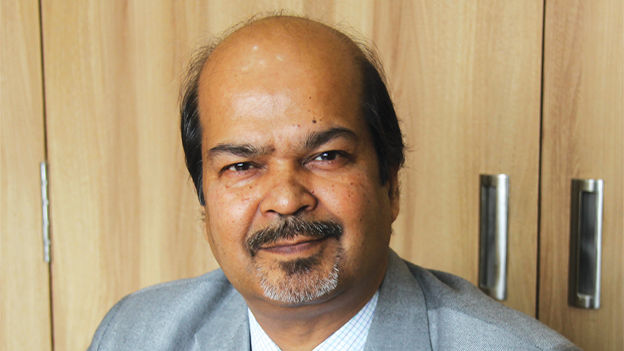
India continues to be a low-cost economy and there is pressure to maintain low costs and quality delivery even as we deal with inadequate infrastructure and untrained labour
When I started working in the 70s, there was no HR but Personnel & IR and there was lot of engagement with factory workers. Today, that breed has vanished and IR is now left to individual production supervisor on the shop floor who is ill equipped to handle it because he is not trained for this role. There is a skill standard in the IR space also. Several organizations have echoed this view and soon we shall be taking up this development with the help of industry.
Manufacturing output is poised to increase three times in the next 10-12 years with initiatives like the Make In India campaign. This will mean very large number of youth entering shop floors for the first time. We need to prepare for that unfolding scenario. Among other things there is a need to address the IR gap. If we don’t do so, we could have a problem on our hands.
India continues to be a low cost economy and there is pressure to maintain the low costs and quality delivery even as we deal with inadequate infrastructure and untrained labour. So, while we strive to have world-class aspirations, the resources are inadequate and that puts additional pressure on the shop floors. Supervisory cadres play a crucial role here. If we look at the automotive sector, another aspect is the wide gap in working conditions across the value chain. OEMs and large Tier-I manufacturing companies are tending towards world-class, but Tier-II and Tier-III shop floors need much improvement. This also adds to the pressure on the small manufacturing shops.
Labour mobility and Industry Certification
The temporary versus permanent labour has been a big bone of contention in the manufacturing sector. While contract labour has been a solution to cyclical demand, it does lead to issues that sometime snowball and assume ugly proportions. Government’s renewed focus on manufacturing through Make in India and National Manufacturing Policy will throw open need for millions of more skilled workmen.
Workmen currently in the non-formal or contractual employment would find ASDC certification of help. This is industry’s own certification and therefore this will provide an avenue for mobility towards better and permanent employment as demand for qualified workmen increases in the formal sector. Deserving workmen in the non-formal cadres would find this an opportunity to prove their employable skills. Employers would also find this a reliable measurement of employability. Through ASDC Certification, organizations can assess the level of skill and competence of these workmen. This can be used to take hiring decisions based on National Skill Standards for specific job roles. Of course, there would be need for fresh labour entering the manufacturing sector. There again Training and ASDC Certification would offer a reliable data for hiring decisions.
One aspect of labour legislation also deals with apprenticeship schemes. There is a need for reform there. Major manufacturing nations like Germany and Japan have found that these apprenticeship programs are a great way to attract, train and retain people. Our understanding is that the government is working on this issue and we expect more practical approach that would actually help labour in improving their prospects in the market.
Contractual work could provide opportunities for on the job apprenticeship for fresh talent. Even the unions should promote this certification everywhere.