Retain your critical workforce to bounce back post lockdown: Rajeev Kaul
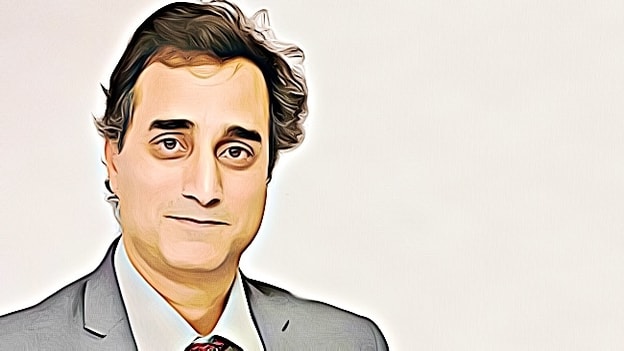
The COVID-19 pandemic and the subsequent lockdown has severely impacted the commercial aviation sector. With aircrafts grounded and workers sent home, the sector is currently witnessing disruption in production along with a slowdown in demand. Globally, this impact on commercial aviation led to a ripple effect on aircraft manufacturers as customers have reduced their orders and deferred delivery of new aircraft.
To understand more about the business and people challenges faced by aircraft manufacturers amid COVID-19 crisis, we interacted with Rajeev Kaul, MD and CEO, Aequs Aerospace.
How has the COVID-19 pandemic impacted your sector? What are the top business and people challenges it has brought with it?
Considering that aircraft manufacturers are capital intensive by nature, the current global health crisis raises short-term concerns about cash flow and liquidity. In the long run, these cash flow shortages and production challenges could have a cascading effect throughout the supply chain. This might weaken the industrial base that supports complex manufacturing processes. It also means that companies might lose their market share if they fail to meet their customer deliverables or if they are unable to invest in new products during this period. Additionally, the risk of critical program failure is likely to rise. Key suppliers and specialized solution providers may further be financially stressed and would require support from companies and the government to stabilize their businesses in a post-COVID-19 world.
Aerospace and defence companies are also going to be defined by their actions and steps taken to respond, recover, and grow. As an immediate first step, companies must retain their critical workforce consisting of highly skilled employees.
The second step would be to identify and support key suppliers and ensure adequate liquidity for them, along with strategic cost optimization. It is also imperative that manufacturers explore alternate supply chain strategies during this difficult time.
How are you dealing with these challenges? Do you have a business continuity plan in place? If yes, can you share more about it?
We have resumed operations in a phased manner and have deployed the highest standards of industrial hygiene and safety protocols across our SEZ in Belgaum, Karnataka.
The plan is to gradually ramp up production capacity to meet the critical part requirements of our customers. The company has been working towards ensuring minimal disruption of operation while simultaneously protecting our employees from any potential exposure to COVID-19. Our teams across manufacturing, engineering, supply chain, and project management are prioritizing customer requirements and have been planning operations accordingly.
We are closely monitoring the situation and have set up a dedicated task force to ensure that the safety protocols are being followed at every level in the organization. Additionally, we have a detailed containment plan to immediately curb the potential spread of the virus within our facility, if any, in the future.
How are you managing the transition to the new normal of work?
The pandemic has surely changed the way we look at people management, operational priorities, and safety. These should remain as key priorities for the companies during this lockdown period.
As the world prepares for the ‘new normal,’ business leaders must rethink strategies in order to build their resilience and come out of this crisis stronger. While business activities that require physical interactions have suffered, the pandemic has presented opportunities to explore new ways of working in the contactless, digital world.
We must revise business plans, including growth earnings and budgetary allocations. There should be a deep focus on customer retention by maintaining a high quality of products and services. It is also important to preserve capital by spending wisely and ensuring positive cash flows while withstanding our values of transparency, trust, and respect.
Has this crisis impacted your leadership style in any way? How do you think you are transforming as a leader?
The current scenario demands that we think out-of-the-box. While the fundamentals of adaptability and agility continue, with preparedness we need to identify new ways of thinking and problem-solving.
As leaders, we must continue to focus on what we have been doing so far, rely on our strengths to drive the goals such as cost optimization, keep in touch with our customers, manage our workforce and steer visibility during these uncertain times.
We must continue to engage the overall business ecosystem and strengthen our supply chain with the bigger picture in mind. However, we do understand the intricate connection between the leader and the employees. A focused approach on deliverables, along with compassion and empathy towards employees, is what will ensure business continuity.
The world is in crisis, and leaders must embrace safety and hygiene practices as a norm on the shop floor and workplaces going forward.
What are some critical choices that you have had to make in this time of crisis? How did you deal with them? If you can share your story.
The impact of COVID-19 pandemic is evolving by the minute and has affected our lives, workplace, communities, and homes. With the situation continuing to unfold with several unknown elements in play, it is challenging to see what the future will hold. However, the global aerospace and defence industry has witnessed immediate consequences in terms of reduction in customer orders, production, and delivery delay.
Companies must take a step back and look at their processes critically in order to understand the bigger picture.
At Aequs, we have established a dedicated committee to monitor this situation closely and communicate the same to internal and external stakeholders. Additionally, we have been taking steps towards maintaining positive cash flows, and as an initial step, we have put a hiring freeze until things stabilize. Additionally, we have streamlined all our manufacturing processes to reduce redundancies while maintaining productivity on the shop floor with a limited workforce.
We are aware that our customers are under constant pressure to innovate, adapt, and overcome industry challenges and are facing an unprecedented shift in the market. These challenges require us to rework our business model, supply chain, adopt digitization, and execute cost-optimization exercises. We will continue to work with our customers during this process and enable cost optimization and adhere to the delivery schedules.
We stand in solidarity with our global engineering and manufacturing partners during this time of crisis and remain focused on recovery and regrowth.
Do you think that post pandemic trends like remote working, flexi hours become a common trend? What other trends at work, do you think are here to stay? What would it mean for your sector? How do you see it happening in reality?
Work from home and other flexible working approaches are being considered as the right approach by the majority of employers.
However, these approaches have limited value in the manufacturing industry, as shop floor operations are pivotal to business continuity. We must resume production on-ground while following high standards of safety and social distancing. A flexible working policy can be adopted by the non-sales workforce of the company whose physical presence is not required for operations.
How do you think digital transformation will be impacted? Will the organization’s structure become leaner? How will the demand for talent change with this?
With digitization becoming an inevitable need today, companies must act quickly to ensure that they have the systems, processes, and support staff in place to enable a seamless transition. As employees work virtually, companies must also strengthen cybersecurity measures while planning for bandwidth, VPN, infrastructure, authentication, and access controls.
The organization can also make its structure leaner and more agile by maintaining a critical workforce of highly skilled people. The safety and health of these workers must be protected with best practices as they use their skills to optimize productivity on the shop floor. Another way to become leaner during this difficult time would be to understand specific functions and teams that can work remotely. This will ensure that only essential staff is on-ground.
The demand for talent is also expected to evolve with this transformation. Organizations will be looking for talent with the right technical skillset to lead this change.
What would be the key roles and top skills in demand? How are you preparing your employees for this new future of work?
India is now being considered as a global hub for aerospace manufacturing offering globally competitive parts. The aerospace manufacturing industry follows a ‘zero-error’ policy; this demands highly specialized skills for critical processes and an effective workforce that can act as a key differentiator. Considering the novelty of this niche and aspirational sector, there is a scarcity of aerospace centric education and vocational training in engineering colleges; training and development play an integral role as the employees have to be upskilled at regular intervals to stay relevant and meet global quality standards. This will help aerospace companies meet the growing demands and stay ahead of the competition.
In order to address the deficit in specialized skills required in aerospace manufacturing, especially in critical operations like machining, forging, turning and milling, surface treatment, and quality inspection, we have introduced a systematic turning program to nurture in house talent.
The new future of work is bound to create a modern workforce that has been upskilled to meet dynamic requirements with the help of digital processes.
Therefore, it becomes essential for aerospace workplaces to incorporate radical thinking, new technologies, and zero-defect processes. By prioritizing innovation and people, aerospace workplaces can soar to higher altitudes.
Lastly, how are you dealing with this crisis? What are some personal challenges you think leaders often face in these tough times? How are you ensuring that you keep calm, sail through and help others also in these tough times? Share your tips.
These are challenging times, and everybody has been affected, either directly or indirectly. On an everyday basis, I keep an eye on the progress of the situation globally and keep a close tab on the wellbeing of our customers. Besides this, I am in regular touch with our employees to ensure their safety and health.