Emerging job roles and skills in the manufacturing sector
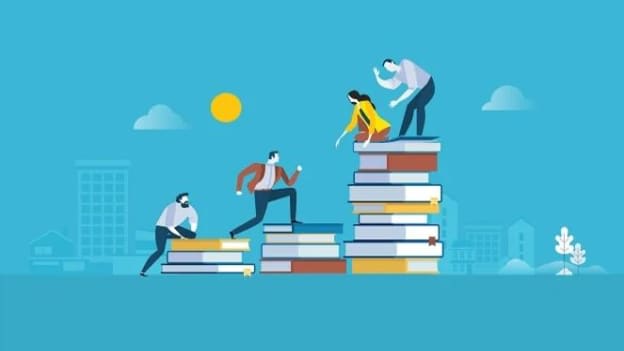
Change, evolution and transformation are buzz words that have become common parlance in the corporate world. However, as cliché as they may sound, when we reflect on our own journey, we do realise, there is absolute truth in them. Our skillsets, ways of working, culture, concepts of leadership that were revered in the past have completely changed in order to stay relevant. As our country and business landscape changes, so does our response to survive and excel. 2020 saw a huge impetus on new age technology accompanied with workplace transformation.
Mostly, when we think of any new- age technology and approach, our imagination gets restricted to the services and IT organizations, because as end-users we experience them more regularly. When we think of manufacturing, the first few thoughts that come to our mind are industrial relations, lean processes and basic problem- solving. If we just take a closer look at how industrial revolutions have made significant breakthroughs in the way we work in order to give a flawless customer experience, it gives us a different perspective on the future of the manufacturing industry. It started with mechanization through water and steam power, wave two saw mass production and assembly lines powered by electricity, followed by computerization and automation, so what next? The overarching theme of Industry 4.0 often referred to as 4th industry evolution with its Smart factories and cyber-physical systems possibly seems to be the future for the manufacturing sector. The manufacturing sector has started adopting the digital age and many progressive organizations are seeing a real impact, through automation, robotics or IoT technology to track all processes in an automated way.
Several reports, and insights by experts from Deloitte and McKinsey highlight that demand for technological, social and emotional, and higher cognitive skills will rise by 2030 and will impact all industries alike. The adoption of automation and artificial intelligence (AI) has accelerated change in skill relevance for success. Impact of such adoption is likely to disrupt production functions in factories through better analytics and increased human-machine collaboration. Future belongs to Smart Factory Manager, Smart Safety Supervisor, Smart Scheduler, Smart Quality Manager and Drone Data Manager. Thus, organizations have a lot to think about in terms of talent and skill-building. Are we ready to embrace this change not merely in talent profile but in our mindsets, ways of working, and investments?
- Digital Skills for new age automation - Organizations have been forced to reimagine how they evolve their workflows and processes differently with changing times. The future of manufacturing is still continually being created, we can’t predict it, but we can sense that transformations will be seen in areas of supply chain and operations to enhance productivity and customer experience. AI, IoT, Big data, virtual and augmented reality, robotics will see a higher rate of adoption in work processes. As companies adopt new, digitally enabled approaches across their operations, Employees will have to acquire skills and get adept at using data, AI-connected systems, and robotics tools. Employees must also build the capacity to adapt to new technologies constantly.
- Data is the new Oil! - In the era of the data economy, the competitive advantage has shifted from only having product or strategy differentiation to how efficiently we use data to make choices and course corrections that impact customer experience. Big data, modern statistical software and tools are generating opportunities to use data analytics real time with sophisticated analysis. The focus is shifting from basic problem solving to focussing on proactive and creative solutions based on predictive analytics. While interacting with some of the operations leaders, it’s interesting to learn that they are looking at leveraging data to learn the interplay between parameters to make more relevant, proactive and cutting-edge decisions; basic examples in Quality going beyond SQC. Clearly, data mining, crunching and analysis is gaining significance and owing to such trends demand for higher cognitive skills will see growth
- Man-Machine collaboration - If the way forward is clearly signalling the adoption of new-age technology and automation, it has huge implications even on our shop floor workforce. They will be expected to learn and adapt to technology and new ways of working. Organizations will have to focus on upskilling them on basic technology, language and troubleshooting skills and capability. If we will not elevate this workforce, it runs the risk of elimination in the future.
- Manufacturing roles with higher appreciation for market and customer - Customer centricity is driving all our decisions and strategies. To accomplish this vision, all functions must play a pivotal part in collaboration and accountability. Manufacturing can no longer be seen in a silo as a backend function and can play a very strategic role in commercial success by leveraging technology, predictive analytics, big data and agility. Similarly, the operations team too has to take a leap forward and be an integral part of the business strategies, commercial and product decisions.
- Leadership will get tested and many styles will emerge - Very often we associate manufacturing with managing a large workforce with a higher proportion of blue-collar workforce. The talent landscape and skill requirements owing to the technological advancement and evolution is changing. That being the case, management and leadership style will need to be flexed. Leaders will have to think of ways in which they will engage and coach the new- age talent. Leaders who continue to operate with archaic ways of thinking, rigidity accompanied with lack of empathy, are increasingly finding it difficult to survive. The much-needed values of compassion, empathy, openness to co-creating strategies and ideas to innovate, are showing better success and assuming higher significance as leadership attributes.
The acceleration in the changes that we have witnessed in recent times has impacted three major work dimensions ─ the workforce and the workplace and the work itself. The consequences of these changes backed, by mass adoption digital platforms and technology at large, can be observed at all stages of business. While the organizations are aiming to ensure business continuity, in times when consumers are comfortable with the increased use of technology, emergence of new job roles and skills is certain. Although the degree of emergence may be varied depending on the industry and the readiness of the companies to make huge investments, the COVID-19 crisis has certainly acted as a catalyst, especially in building resilience among businesses for future disruptions. The manufacturing industry is at the doorstep of a potentially pivotal transformation amid the technology enabled interaction of the workforce that itself will revamp as we move ahead. Manufacturing units will be transformed into smart manufacturing units. We are heading towards improved synchronisation of the business processes as well as the workers executing those processes.