Cobots carving an ergonomic, sustainable future
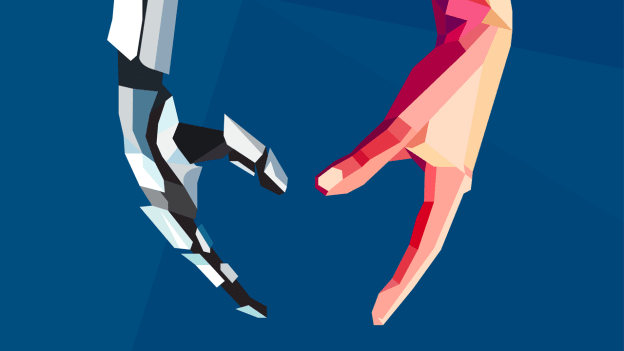
From the physical design to the equipment used, the workspace is one that poses a multitude of risks to its employees. Many jobs, especially in the manufacturing industry, present ergonomic risks to its workers by putting them through repetitive movements, equipment-handling, or physically taxing work.
In India, it is not uncommon for the blue-collar workers tend to extend their working hours in factories and manufacturing units to earn some extra income. Little do they know, however, that they are actually running the risk of injury by engaging in such labor-intensive work.
Tasks like loading and unloading of bulky goods, working in an unsuitable environment or unhealthy conditions could result in a lifetime risk, injuring one irreversibly.
As safety in the workplace is paramount and worker rights are increasingly given more attention, the tech industry is witnessing the ascent of the collaborative robot, or cobots. Cobots were created to share the same physical workplace as humans, with special technology that enables a protective stop if the cobot comes in contact with a person, thereby preventing any harm. Manufacturers are increasingly turning to cobots to reduce ergonomic risks on the factory floor by taking care of dull and repetitive tasks. Cobots reduce monotony at the workplace as they consistently and efficiently manage tasks such as pick and place, bolt-tightening, and palletizing, collaborating with employees who then are taught to supervise their cobot colleagues. In fact, according to an MIT study, this human-robot collaboration facilitated by cobots improves productivity on the shop floor by approximately 85%.
Beloved Indian bike manufacturer Bajaj Auto Ltd. is a testament to this. With over 100 cobots – which were also the first collaborative robots in India – the company integrated cobots at its Chakan plant to handle a range of repetitive tasks on their assembly line, which used to all be done manually before. With a 50% female workforce, Bajaj found cobots especially useful in empowering their women workers to oversee physically taxing work, such as bolt-tightening, which previously caused strain and fatigue to employees.
L’Oréal India is another such company that found cobots to be the ideal solution for its safety concerns. Following a risk analysis, the company found a Level-4 ergonomic risk posed by manual palletizing, a process in which employees lifted up to 8,500 kgs a day. The FMCG giant turned to cobots, and completely eradicated the ergonomic risk by automating the palletization with collaborative robots. Plus, they even witnessed a 5% increase in Overall Equipment Efficiency, as they were able to fill two pallets at a time, instead of just one.
Even Indian SMEs and MSMEs are now starting to recognize the significance of cobots, which allow for partial automation by catalyzing interdependency between man and machine, and are thereby affordable and accessible. With high accuracy and speed, they allow manufacturers to optimize quality, consistency, productivity, and even variability that traditional robots simply cannot facilitate.
Aside from their ability to safely work with humans (subject to risk assessment), they present an unparalleled ease of operation through a teach pendant, i.e. a touchscreen device that virtually anyone can use to learn how to program a cobot within a day. Deployment and installation can be completed within hours, making it easy for workers to initiate their tasks and complete them timely and efficiently, eliminating long hours of downtime. Indian SMEs like New Engineering Works, Jamshedpur, has even begun upskilling their labor force to learn more meaningful tasks, since cobots are now handling the mundane work.
This seemingly futuristic concept of human-robot collaboration facilitated by cobots is taking the manufacturing world by storm, and even thought to be part of the wave of “Industry 5.0,” or collaborative industries, reflecting a growing view amongst manufacturers of the need to respond to increasing demand amongst customers for a higher degree of individualization. Eighty-five percent of manufacturers consider the “connected workforce” - that is, robots and humans working together – to be routine in manufacturing by 2020. In fact, an overwhelming majority of manufacturers even describe it as an essential element in their business strategy.
Cobots enable companies to bring the human touch back to production and manufacturing. This is by encouraging and enabling a scenario where the technical capabilities and consistent repetitiveness of a robot are used to reduce production times, boost accuracy, and improve product/finish quality, all while reducing risk of injury to the worker, who now has the time to focus on other aspects of work that actually require human effort. Human employees can therefore apply their intangible skills and difficult-to-program creativity to more complex projects – or to notch up a considerable boost in productivity for their particular craft or profession. This, in turn, makes it possible to comply with new kinds of market requirements and consumer expectations, often involving greater personalization to individual preferences.
The future is now with collaborative robots, which are reinventing and reshaping what robotics once meant in the manufacturing world. By allowing man and machine to collaborate and focus on what each one of them do best, safely, they allow for a unique relationship that is all set to create an ergonomic and sustainable future.