The biggest pain point in manufacturing? Loss of productivity due to absenteeism: HONO has a solution
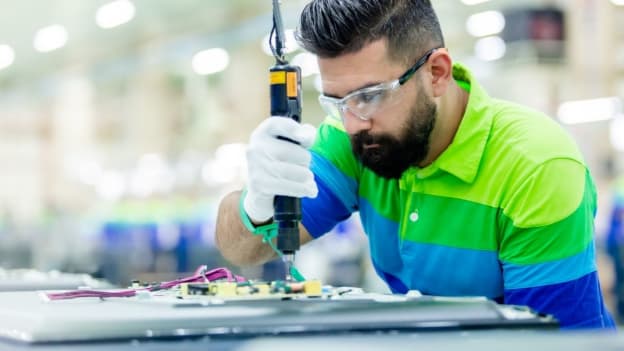
It's another day at the factory and hundreds of workers are about to pour in. An hour into the shift, line managers begin to notice production lines are slower than usual. What could be causing the delay?
The case: a number of workers are unable to report to work for reasons beyond their control, and their absence is debilitating production. For workforce managers, it's an all-too-familiar story.
In the increasingly complex environment of the manufacturing industry, the goal of ensuring all segments of the workforce are on time and on track with their production is paramount to success. One area where most manufacturers continue to struggle, however, is that of responding to abrupt changes in manpower, such as when circumstances outside of work prevent staff from coming in for their shift.
And it's even more challenging when those crucial manpower changes happen at the last hour.
The wave of unplanned absenteeism
While factors behind unplanned absenteeism are varied and complex, how organizations respond to disruptions in their manpower spells the difference between successfully minimizing the impact of low attendance on productivity, and suffering productivity loss altogether.
Unplanned absenteeism in labor-intensive industries triggers productivity losses, given the sequential nature of production. When a line experiences worker absenteeism, "segmental delays become bottlenecks that ultimately impede productivity," according to research published in Ideas for India.
Once average absenteeism reaches 10% in labor-intensive settings, productivity begins to decline. For every percentage point that absenteeism rises thereafter, productivity falls another 0.25 percentage points, findings of the study showed.
In India, unplanned absences can cause a productivity loss of as high as 35.5%. Respondents report unplanned absences can disrupt the work of others (65%), add to the workload of others (64%), increase workers’ stress (47%) and reduce the quality of work output (45%), among other negative effects, according to a study led by the Society for Human Resource Management.
Factory line managers would often be forced to borrow, lend and redeploy workers across different production lines to close gaps in staffing and bolster activity. However, this tactic of redistributing workers comes in response to challenges, only as they unfold and after a significant productivity loss.
To address unplanned absences better, line managers need predictive and real-time dashboards that give them an overview of their manpower, and how the labor supply matches the demand.
This is where HR, workforce and plant managers benefit from having visibility into the roster, down to the minute when employees walk in.
Beyond attendance tracking: The HONO solution
In the face of unplanned absenteeism, managers require technology-based and data-driven support to carry on quality work efficiently. One practical method is to use a predictive solution that plugs the gap in the roster, as reported by line managers at the start of each shift. The solution is designed to find replacements, with the desired skill set mapped to the line, who are either on standby or working on a low-priority line.
Beyond everyday staffing challenges, some of the most pressing questions on manpower that confront employers today center on:
● The ability of employers to reduce inaccuracies in workforce data to help them make better decisions on staffing
● The opportunity of employers to respond to gaps in the roster through the aid of automation, otherwise known as auto-rostering and auto-replacement
● The ability of managers to plan the roster, manage disruptions, and increase efficiencies
Specialized in driving disruptive productivity solutions for manufacturing, HONO has been helping employers address the challenge of unplanned absenteeism, among other workforce challenges.
HONO has developed a comprehensive signature Productivity Management platform powered by artificial intelligence, which offers a range of solutions – from Auto-Rostering and Auto-Shift Management to the Employee Absence Predictor and Auto-Replacement, to the touchless Employee Access Control.
With these streamlined solutions, employers can respond to manpower disruptions and redistribute resources automatically to protect productivity targets even before the start of each shift.
HONO's Early Warning System, which confirms the arrival of workers before the shift starts, plays an integral role in keeping count of workers more accurately and in monitoring gaps that need to be filled urgently that day. The beauty of the disruptive solution kicks in at this stage where it also does auto-replacements based on the skill mapping.
HONO isn't your average manpower tracking system. To succeed at automating the shift management and absentee replacement process, the platform goes further by using comprehensive workforce management data built from the ground up. It involves skill mapping, line mapping and position mapping – which help employers identify and analyze potential skills gaps in the workforce and to plan training and development initiatives accordingly.
Skill mapping entails looking at individual skill sets as an asset and mapping them out into the AI Engine. The system aligns with the needs of different work lines. This matching of existing skill sets – against the requirements of business units or functions – is called line mapping. Meanwhile, each job position is mapped out in the context of these skills and work lines in a process called position mapping.
We can think of the organization as a complex machine with many moving parts. Employers will thus need solutions that keep track of all those movements. HONO provides this for organizations.
“If business leaders believe data is power, then now is the best time to wield the power of real-time workforce data – not only to predict and respond to staffing challenges, but also to buffer the impact of productivity losses on the company's bottom line,” said Mukul Jain, founder and CEO of HONO.
“Optimizing workforce management with data has become critical because failure to do so leads to increased financial losses, increased compliance and legal risks, and major disruptions to production schedules and delivery timelines. All of which can be addressed if the issue of absenteeism is managed, delivering for companies increased business performance and customer satisfaction.”
Using HONO’s technology for managing work in this new era, employers in the manufacturing sector can address disruptions while accelerating their productivity and growth. To compete on the world stage, manufacturers that invest in comprehensive solutions are poised to maintain their agility as they reach new milestones. Learn how HONO can transform your business into an organization of the future.